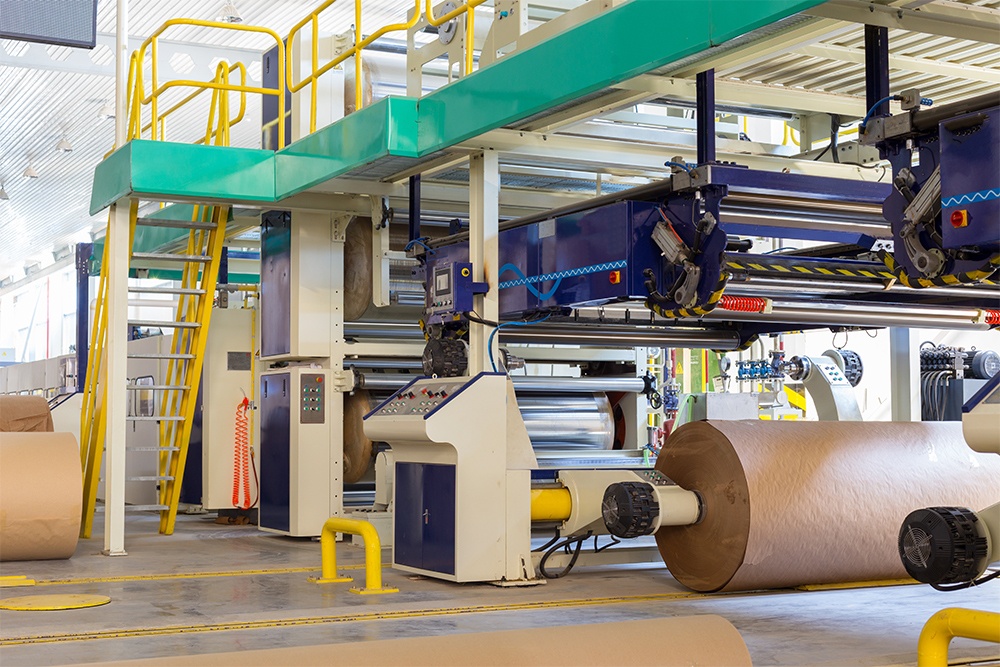
Making sense of your roll alignment options
As someone tasked with looking after roll machinery you understand that proper alignment is vital to keeping your equipment operating efficiently and productively.
Today, however, you are faced with choosing from among a sometimes confusing array of alignment technologies. In this complex marketplace, choosing the best solution for your particular applications and circumstances can be challenging and time-consuming—and mistakes can be expensive!
In this blog, we will go over most of the newer roll alignment technologies to help you evaluate the strengths and weaknesses of each one, and hopefully avoid the pitfalls of choosing the wrong method or system.
We first take a look at common technologies for aligning roll machinery such as paper mills, film lines, printing presses, textile mills and aluminum and copper foil mills—and then compare them with our unique and highly accurate roll alignment systems manufactured by Hamar Laser Instruments.
Common Alignment Problems
As many of you have experienced, poorly aligned rolls can cause a number of very serious problems, such as product “wandering” off the rolls, wrinkling, tearing or even breaking completely, all of which can lead to excess downtime and increased scrapped product.
Complicating the solution to the problem, optical-based alignment methods that are typically used to install machinery are often not the best solutions for periodic alignment checks because they require using the “permanent” floor-mounted brass monuments to establish the “offset centerline” reference. The problem with floor monuments is cracking, settling and shifting of “hard” concrete over time, which causes significant shifts in the monuments’ locations, leading to significant alignment errors. In addition, vibrations from normal operations can cause many machines to gradually shift from their initial position relative to the floor mounts, producing a similar result.
Comparing Alignment Technologies
Fortunately there are several roll-alignment technologies available that can do a much better job with roll alignment than the “tried and true” set of optics. So let’s take a look at 4 of these technologies (see table):
- Pentaprism or “beam-bending” lasers – Use 2 tripods, 1 to hold the laser and 1 to hold a moveable pentaprism fixture that bends the beam 90 degrees to measure the rolls.
- Laser-trackers – Use an expensive and highly technical triangulation method to track a retro-reflector ball fixture that measures the rolls relative to pre-established references.
- Gyroscope-based technology – Uses a military-grade gyroscope technology to measure the rolls relative to the earth’s rotation.
- Multi-plane, auto-rotating lasers – Use 2-3 auto-rotating laser planes that are square to each other and portable reference target fixtures to very quickly and accurately move the laser from one section to the next to measure the rolls.
Pentaprism Laser Technologies
A number of companies manufacture laser-based alignment systems that are designed around pentaprisms. Most of these devices use manually rotating laser planes with pentaprisms that “bend” the laser beams 90 degrees in order to make them parallel to the reference laser. While all of the various pentaprism devices have been designed around similar technology, we find that some perform better than others.
Virtually all of the laser-based technologies, including those utilizing pentaprisms, have the advantage of being somewhat faster than conventional methods, such as optics, and are far less expensive than gyroscope-based systems and laser-trackers.
However, these pentaprism laser systems have a number of disadvantages:
- They require complicated, time-consuming set-ups and specialized software, and typically need 2 optical technicians to operate them.
- Their technology relies heavily on the accuracy of their pentaprisms, and since they use 2 pentaprisms, one built into the laser and the second into the pentaprism fixture, their squareness errors “stack up” and this negatively impacts the roll-to-roll parallelism accuracy their systems are able to achieve.
- These lasers do not automatically rotate, so the user has to manually rotate the laser turret to point the laser beam toward the detector (target).
- Their measurement errors are significant due to too many optical components.
Here’s how these errors can significantly impact the measurement accuracy:
- The squareness error of the laser is 0.02 mm/m. The laser is aligned to the reference roll and its perpendicular laser beam points down the side of the machine to serve as the “offset centerline” of the machine.
- The squareness error of the portable pentaprism fixture is 0.02 mm/m. This fixture is mounted on a tripod and positioned down the machine in a section of rolls to be measured. The pentaprism fixture is aligned by eye to the laser beam and it bends the beam 90 degrees to measure the rolls for parallelism. This results in a combined roll-to-roll parallelism error of 0.04 mm/m, which isn’t too bad but isn’t good either.
- The laser step error is up to 1.0 mm (.040 in.). To use a pentaprism fixture, you must center the fixture to the laser beam using a visual target, which means a “resolution” of 0.5 mm (the best the eye can see). If the axis of rotation of a rotating pentaprism is not aligned to the laser, users get a 2-to-1 translation error relative to the centering error in a 180-degree sweep, so a 0.5 mm centering error turns into a 1.0 mm laser step error. This means that when users rotate the laser beam in its pentaprism fixture to reach rolls above or below the fixture, they introduce a potentially very large step error into the measurement. (See our brochure for details.)
This means pentaprism-based roll alignment technology could have significant measurement errors if the user is not careful. While end users may benefit from their use of laser technology, the shortcomings of these pentaprism systems become even more apparent when they are compared against multi-plane, automatically rotating alignment systems manufactured by Hamar Laser, as we will discuss in a moment.
Laser-Tracker Technologies
Laser-trackers can be a very accurate technology in the hands of a well-trained engineer and are typically used for complex machine installations where measuring the X-Y-Z location of components is important for assembly and startup. They can also be used for alignment.
One of the main disadvantages of laser-trackers is the high degree of training and skill required to run them. To achieve good and accurate results, either a highly skilled technician or engineer is needed to run the system and software. While this might work for new installations where downtime is not an issue, it is not a very efficient method to use for typical maintenance requirements, where the degree of skill of the operators is lower and minimizing downtime is paramount. Easy-to-make mistakes can lead to costly extra downtime and product waste.
Another very important disadvantage for laser-trackers is their high cost, which can be 2-3 times higher than other laser-based technologies. Laser-trackers certainly have their place, but not in a maintenance department tool crib!
Gyroscope-Based Technology
Gyroscope-based alignment systems are based on an advanced military-grade gyro technology. The system’s advantages are that it has a fast setup and takes measurements for both levelness and parallelism very quickly. The typical resolution of these systems is specified at 0.008 mm/m. However, specifications for accuracy are not available, making it difficult to evaluate how accurately this system can actually align rolls.
These advantages are offset, however, by a couple of significant disadvantages:
- The system is prohibitively expensive for many would-be purchasers. In addition, export restrictions on military grade gyro technology limit the availability of the device for sale in certain areas, including the USA. For this reason, the technology is typically only offered as an alignment service using the device but at a very high hourly fee.
- The gyro system does not provide real-time measurements and instead gives the user a roll alignment report. When offered as a service, this requires follow-up visits after adjustments are made to the alignment of machine’s rolls to verify the alignment. With high hourly fees, this can significantly increase the overall cost for the alignment of each machine. In a lot of cases, the annual fees are high enough to easily justify purchasing a laser-based alignment system.
- It’s sometimes hard to schedule alignment services when machinery fails. Downed manufacturing lines are more likely to be up and running much sooner if the alignment equipment is in house.
Given that there are lower-priced laser systems available that can both measure and provide real-time data to align the rolls, it makes much more sense to spend hard-to-get investment dollars on laser-based systems that can do the whole job, or contract with a service vendor who uses them.
Multi-Plane Laser Technologies
Among laser-based technologies, advanced multi-plane, auto-rotating laser alignment systems are in a class by themselves.
A pioneer in laser alignment since its founding in 1967, Hamar Laser introduced the first automatically rotating laser plane in 1985. Today, Hamar Laser is the only company in the world able to offer alignment systems featuring multiple automatically rotating laser planes that are ideally suited for roll alignment and offer significant advantages over older conventional methods, gyroscope-based and pentaprism-based laser systems and laser-trackers.
Depending on the roll-alignment accuracy requirements, for most common roll alignment applications Hamar Laser offers (see sidebar):
- L-742 Ultra-Precision Dual Scan® Roll Alignment System
- L-732 Precision Dual Scan® Roll Alignment System
Accuracy
Unlike pentaprism-based systems, which rely heavily on the squareness of the laser plane and pentaprism, the unique design of Hamar Laser’s Dual Scan® systems, featuring 2 automatically rotating lasers planes, effectively eliminates squareness errors. This results in the L-742 being up to 9 times more accurate than currently available pentaprism-based systems and up to 4 times as accurate as optical theodolites.
The variability in measurement that results from operator to operator using the L-742 or L-732 is significantly less than optical or pentaprism-based laser systems, so the measurement repeatability is excellent.
Speed & Utility
The L-742 and L-732 set up faster and are easier to use than pentaprism-based laser systems, laser trackers and optical systems. They can be used by a single optical technician, rather than an engineer or multiple technicians, reducing manpower and training costs. It typically takes 2 days to train someone to use the L-742 or L-732 versus 1-2 weeks for optics or trackers.
Hamar Laser’s solutions are the only laser-based systems designed to be used with up to 5 wireless targets which simultaneously transmit their data to a rugged PDA readout. The use of these multiple targets greatly speeds up the transfer process during alignments, minimizing time and labor investment. It also allows multiple rolls to be measured simultaneously from the same setup.
The L-742’s and L-732’s automatically rotating laser planes are effective up to 100 feet in any direction, so machine rolls up to 200 feet apart—in any elevation—can be aligned without repositioning the laser. In fact, with our transfer method, there is no limit to the length of machines that these systems can align!
Versatility
Add in a 3rd laser plane for leveling, and the Dual Scan® Roll Alignment system turns into a Triple Scan® L-743 or L-733 that can measure flatness and levelness of surfaces. The L-743 and L-733 can also be used for many other applications from machine tools to aerospace.
Click here to see a typical roll alignment procedure using the L-742 or L-732.
Choose the Best Option for Your Needs
We hope this information has been helpful. Because each alignment situation is different, we recognize that our system may not always be the best choice in every circumstance; however, we believe strongly that for the majority of applications an L-742 or L-732 Roll Alignment System from Hamar Laser will provide the best results and value for your investment.
As with any other important purchase, you want to do your homework and make sure you are buying the best system for your needs—and not paying too much in the process. Today, multiple alignment options are available to you, with some high-end systems costing a large amount of money. For a fraction of the price of those systems, a laser alignment solution from Hamar Laser can get the job done as well or better, with less skilled operators and perform the actual alignment.
For further information about roll alignment using Hamar Laser’s proven, innovative solutions, or to schedule a free demo, please visit our website at www.hamarlaser.com or contact us with your questions at sales@hamarlaser.com or +1-203-730-4600.
With more than five decades of experience, we can truly say
“We understand roll alignment!”
Wow! this is very informative and helpful ideas. Thank you for sharing this.
Mitsubishi laser parts
Sir we are plaster board manufacturer ,we want to do alignment of roller (Paper stand to setting belt ) There are around 20 roller are there in length of 40 meter for that we want to do alignment
to provide us knowledge
We want to make arrangements for 12 rollers which are 2800 mm in length and 100 to 250 mm diameter. Use for blown film plant.
You are partially correct on the gyro based alignment. 1st the accuracy is 0.005 mils per foot on our device, 2nd as a service we can measure in excess of 100 rolls and support adjustments while on site to include remeasuring adjusted rolls after adjustment within an eight hour day depending on the application as well as provide an almost instant final image at the end of the day, 3rd this service may be a little expensive but no line of site is required and the measurement process is extremely fast.
Thanks for the comment. There is NO WAY your accuracy is .005 mils/ft. That is .000005 in/ft which is 10 times higher than your stated resolution of .00005 in/ft. That is impossible. Accuracy is not the same as resolution. So your accuracy has to be less than .00005 in/ft. Yes of course you can do the measure/move/measure/move process. But to us it’s much better to have the data update in real time so you don’t need to recalibrate the device to get the next measurement. “A little expensive” is a vast understatement for the cost of your service. Hey if you get get it from your customers, good for you, but $10k/day is stiff.